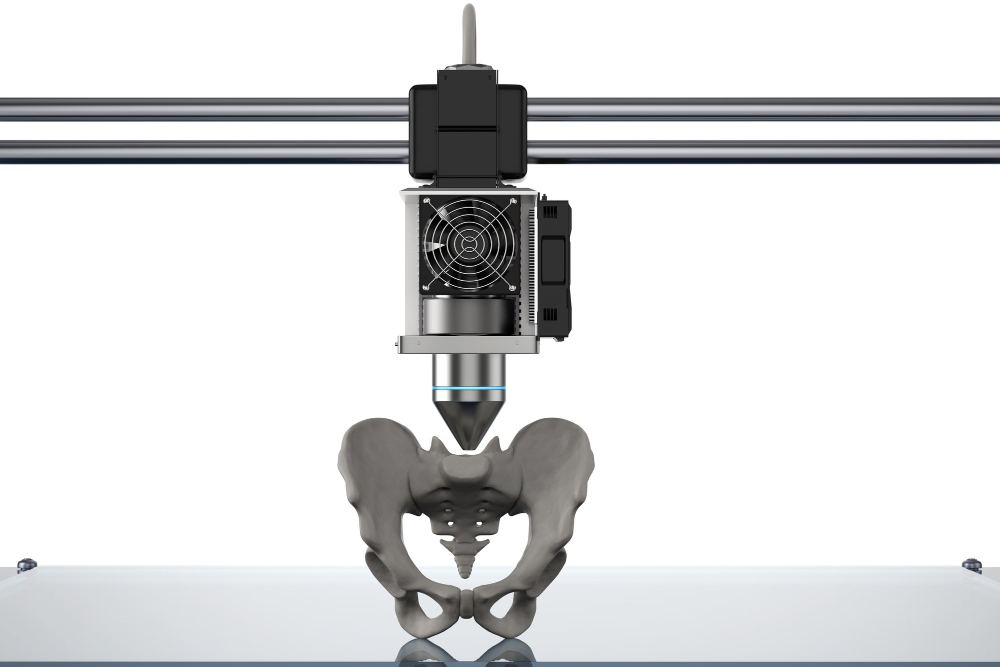
Medical 3D Printing Explained: From CT Scan to Custom Implants
Medical 3D printing has changed from a niche technology into a healthcare revolution. The global market is expected to reach $6.08 billion by 2027. Only three hospitals had in-house 3D printing facilities in 2010. This number jumped to 113 facilities by 2019, which demonstrates rapid adoption of this technology.
The practical benefits of 3D printing in healthcare are remarkable, especially when you have surgical applications. A 2020 study showed that surgeons who used 3D anatomical models as guides reduced operation times by 62 minutes on average. This resulted in savings of $3,720 per case. To cite an instance, see how a surgeon completed a complex procedure in under 30 minutes instead of four hours by using a 3D-printed model.
This groundbreaking technology’s process starts with converting CT scans into precise 3D models and leads to creating custom implants that enhance patient care.
Understanding Medical 3D Printing Technology
Medical 3D printing works in fascinating ways. This technology creates three-dimensional objects layer by layer from digital files that doctors and medical professionals use. The growth in hospitals using this technology has been remarkable. The numbers jumped from just three facilities with in-house 3D printing in 2010 to over hundred hospitals by 2019 [1].
Several printing methods make this technology powerful, each with its own benefits. Fused Deposition Modeling (FDM) leads the pack as the most accessible technique because it’s simple and affordable [2]. On top of that, it uses Stereolithography (SLA) with UV lasers to cure liquid resin, and Selective Laser Sintering (SLS) that fuses powder materials with high-powered lasers [2].
Medical 3D printing’s strength comes from its wide range of compatible materials:
- Engineering-grade polymers
- Biocompatible metals
- Ceramics
- Bioactive materials [1]
This technology gives doctors the freedom to create patient-specific builds that match unique anatomies perfectly [1]. They can now produce complex designs that would be impossible – or really hard – to make with traditional methods. The technology has become essential in creating:
- Patient-specific medical devices
- Custom surgical tools
- Anatomical models
- Research tools [1]
3D printing’s precision and flexibility have created many standards of care in clinical operations. To cite an instance, see anatomical models for presurgical planning and surgical cutting guides that doctors now use regularly. They have efficient workflows to deliver printed products right to the point of care [1].
From Medical Imaging to 3D Model
Medical imaging data needs conversion to printable formats to create 3D models from medical scans. The process starts with CT scans or MRI data stored in DICOM format – the standard file type for medical imaging [3].
The conversion of medical scans to printable 3D models follows these steps:
- Image Acquisition: High-quality CT or MRI scans form the foundation, and their quality parameters affect the final model’s accuracy [4]
- Segmentation: The relevant anatomy gets isolated from surrounding tissues
- File Conversion: STL format becomes the new home for segmented data
- Model Optimization: The mesh errors need repairs and the model needs optimization
- Quality Verification: The model’s accuracy requires verification before printing
The process might look simple, but precision matters at every step. These models guide important surgical decisions, so dimensional accuracy is vital [4]. Model accuracy depends on several factors like slice thickness, reconstruction settings, and segmentation methods [5].
Two approaches can convert these scans. 3D Slicer software provides detailed control over the process. Automated online services offer a streamlined workflow [3]. The anatomy’s complexity and accuracy requirements help determine the best method.
U.S. hospitals with centralized 3D printing facilities have seen remarkable growth. The numbers jumped from three facilities in 2010 to more than 100 by 2019 [6]. This expansion shows why standardized processes and quality control matter in creating medical models.
Manufacturing Custom Medical Implants
Quality control and precise manufacturing define the creation of custom medical implants through 3D printing. Material selection meets strict biocompatibility standards [7]. Medical professionals commonly use these materials:
- Titanium for orthopedic implants
- PEEK (Polyetheretherketherketone) for custom implants
- Medical-grade polymers for specific applications
Quality assurance forms the foundation of our manufacturing process. Our team follows FDA Quality System regulations to produce safe and effective devices consistently [8]. Each production step requires complete documentation that tracks everything from material selection to final sterilization.
The manufacturing process consists of several key stages. Design verification uses pre-specified sizes or patient-matched anatomical models [9]. The printing parameters need careful monitoring because factors like laser power, bed temperature, and scanning speed substantially affect the final product [10].
Post-processing helps achieve the desired implant quality. Our team utilizes various techniques to improve surface quality and eliminate manufacturing residues
[11]. Clean environments support proper cleaning procedures that combine air-blasting with sonication [10].
Sterilization serves as the final vital step, and it needs verification to ensure sterility levels suitable for medical use [10]. The team conducts extensive testing and biocompatibility verification studies to meet all regulatory requirements [8].
Conclusion
Medical 3D printing represents a breakthrough that connects medical imaging with tailored patient care. This technology converts CT scans and MRI data into accurate anatomical models and custom implants. The process has substantially reduced surgical times and costs.
Quality controls and standardized processes make these state-of-the-art solutions dependable for medical use. Healthcare facilities worldwide now experience shorter operation times and better patient outcomes. Their success stems from 3D-printed surgical guides and custom implants.
The future holds more possibilities as hospitals add in-house 3D printing capabilities. Real-life success stories demonstrate 3D printing’s tangible benefits. Surgeons now save valuable time in operating rooms and use better tools for complex procedures.
Medical 3D printing has grown beyond a mere technological innovation. It has become a vital tool that enables medical professionals to deliver enhanced patient care through customization and precision. These developments mark the beginning of an era where tailored medical solutions become the norm rather than the exception.
References
- https://pmc.ncbi.nlm.nih.gov/articles/PMC10734340/
- https://www.novusls.com/post/medical-3d-printing-material-selection-guide?srsltid=AfmBOooIgCCbJDzggT5LcivGTGzAlhC9n8W4d2pNWFwdJ5AYj39WSqOS
- https://ttuhsc.libguides.com/3dprinting/howtoconvertmedicalimaging
- https://www.frontiersin.org/journals/medical-technology/articles/10.3389/fmedt.2023.1097850/full
- https://threedmedprint.biomedcentral.com/articles/10.1186/s41205-024-00210-5
- https://www.pewtrusts.org/en/research-and-analysis/issue-briefs/2020/10/what-is-medical-3d-printing-and-how-is-it-regulated
- https://www.novusls.com/post/medical-3d-printing-material-selection-guide?srsltid=AfmBOorEylItBKL0vjPYtGywt7tbQOlUnArx2GMtf1qo3HDiuyIOFNge
- https://threedmedprint.biomedcentral.com/articles/10.1186/s41205-022-00134-y
- https://www.fda.gov/medical-devices/3d-printing-medical-devices/process-3d-printing-medical-devices
- https://pmc.ncbi.nlm.nih.gov/articles/PMC4626249/
- https://insidemetaladditivemanufacturing.com/2024/08/14/review-of-post-processing-techniques-for-3d-printed-metal-implants/